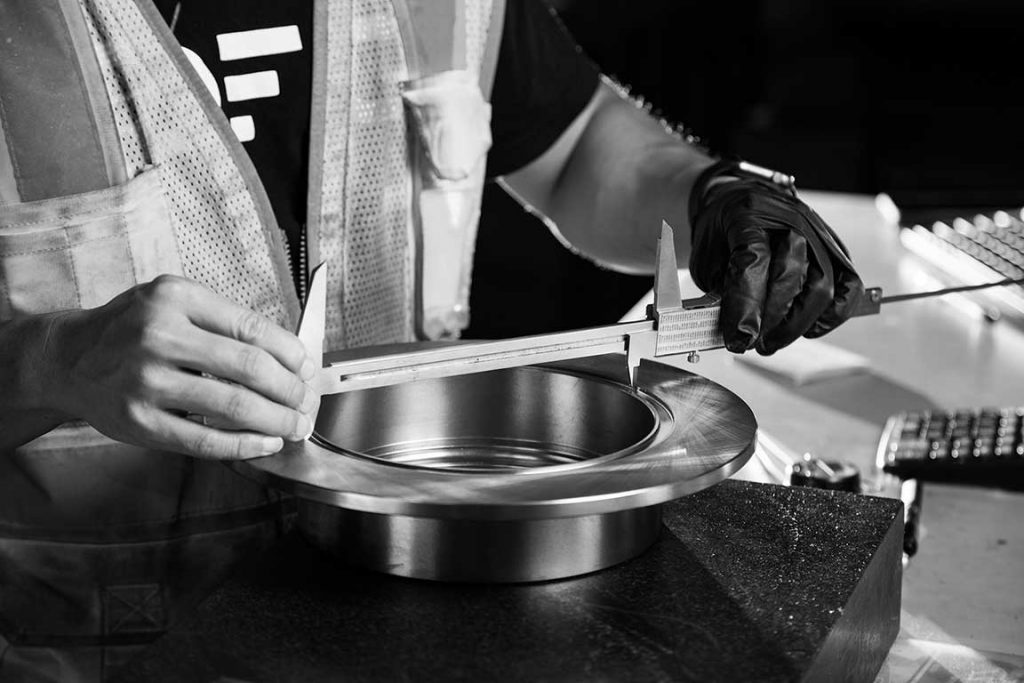
Here at DFC, we take pride in our commitment to R & D.
Our goal is as big as our challenge: to be the leader in developing best in-class brake parts for our industry. Because of this, our products undergo a rigorous research and development process that matches our drive and mission as a company. We invest in top research technology and leverage tools and resources to develop premium quality products that you can rely on.
1. Data Capture
We use state of the art, data acquisition equipment and software in order to measure all dimensions of an OEM part. We do this to ensure that every single product is accurate and faithful to the original design.
2. Modeling & Analysis
DFC uses parametric modeling to simulate real-world performance. We evaluate and optimize all of our designs accordingly, so you get real-world results.
3. Production Drawings
Production Drawings are created in-house, so we own the design and control the fit, the form, and the function of each. This allows us to control and maximize the safety and consistency of all of our parts.
4. Quality Control
To ensure that our end users enjoy a positive experience with our products, we use a mix of manual and automatic processes. Our calibrated measurement equipment and our optical CMM is used for a consistent and objective standard of quality; a standard of quality you can depend on.
Conclusion
At DFC, we use these four main engineering processes in order to give you what you deserve: safety and satisfaction. We’ll help you stop…when you’re ready to go.
Ready for your new brakes?
Click here to see our latest deals