
When it comes to brake calipers, many shops and distributors have relied on remanufactured units in the past due to perceived cost savings. However, hidden inefficiencies, quality issues, and durability concerns often turn those savings into higher long-term expenses. With DFC’s all-new brake calipers, you get consistent quality, reduced failure rates, and competitive pricing—without the headaches.
DFC’s new calipers meet or exceed OEM performance standards, ensuring quality and reliability.
Let’s break down the five key issues with remanufactured calipers and how DFC’s newly manufactured calipers solve them.
1. Core Charges and Return Hassles
Remanufactured calipers require core exchanges, which can add both complexity and unexpected costs. Core returns may not meet acceptance criteria due to issues like corrosion or damage, leading to rejections and extra charges.
With DFC calipers, core exchanges are a thing of the past. Our calipers are all-new, eliminating return hassles and ensuring a smoother purchasing and installation process. Additionally, DFC calipers come with all necessary installation hardware, ensuring easy installation.
2. Caliper Port Inlet Thread Issues
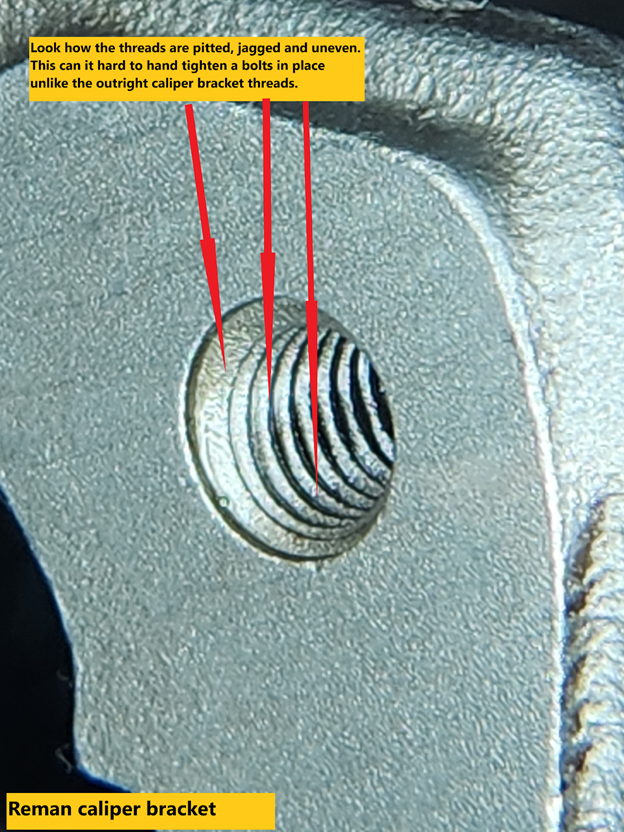
Poorly remanufactured calipers often have pitted, jagged, or uneven threads in the caliper port inlet. This makes hand-tightening difficult, causing leaks and installation delays.
DFC calipers feature precision-machined port threads, ensuring smooth, secure installation without added frustration. This saves valuable time for technicians and prevents potential performance issues caused by improper threading.
3. Challenges with Modern Brake Technology
Electric Parking Brake (EPB) Calipers
EPB calipers integrate the parking brake electronically, eliminating the need for mechanical levers. However, remanufacturing these units is particularly challenging. The complex assembly requires specialized equipment to meet OEM standards, and many remanufactured units suffer from high failure rates due to improper testing and assembly.
By contrast, DFC’s new EPB calipers are built entirely with new components, ensuring reliable operation and long-term durability. Each unit undergoes advanced testing to meet or exceed OEM specifications.
Mechanical Integral Parking Brake Calipers
Similar to EPB calipers, mechanical integral parking brake units require precise assembly to function correctly. Remanufactured versions often fail due to poor quality control, leading to brake performance issues and costly returns.
With DFC, precision-built calipers provide optimal performance and help shops avoid these risks.
4. Corrosion and Surface Damage in Aluminum Calipers
Modern vehicles increasingly use lightweight aluminum calipers, which present unique challenges for remanufacturers. Many rebuilders use abrasive steel-shot cleaning media, which can distort critical surfaces like guide pin bores and brake pad contact points. Aluminum calipers also corrode faster in harsh environments, making them less viable for remanufacturing.
DFC calipers are coated with a premium silver zinc finish to resist corrosion, ensuring long-lasting performance. This protective coating is applied to all our calipers, reducing the risk of surface damage and ensuring smooth, consistent operation. Proper installation of the caliper bracket is crucial to prevent surface damage and ensure the longevity of the caliper.
5. Guide Pin and Seal Integrity
Guide pins and seals play a crucial role in brake performance, but remanufacturing processes often compromise these components. Guide pin bores can become oval-shaped over time, especially in high-mileage calipers. Additionally, some rebuilders blast and tumble caliper bodies with guide pins still attached, causing bent pins and stripped protective coatings. Maintaining the integrity of guide pins and seals is crucial for preventing brake fluid leaks and ensuring optimal brake performance.
DFC calipers come with all-new guide pins, seals, and pin bushings. Our components are engineered to maintain proper alignment and retraction, preventing excessive brake pad contact with the rotor. This reduces wear, minimizes disc thickness variation (DTV), and ensures efficient braking performance.
Proper Brake Caliper Installation is Crucial
The Dangers of Upside-Down Brake Caliper Installation
Installing a brake caliper upside down is a common mistake that can have serious consequences for your vehicle’s braking system. When a caliper is installed upside down, the bleeder valve is positioned at the bottom, making it impossible to properly bleed air from the brake lines. This can lead to air pockets remaining in the system, resulting in reduced braking performance, spongy brake pedal feel, and increased risk of accidents.
In addition to reduced braking performance, an upside-down brake caliper installation can also lead to premature wear on the brake pads and caliper pistons. This can result in increased maintenance costs and reduced stopping power, making it essential to correct the issue as soon as possible. Ensuring the caliper is installed correctly from the start can save time, money, and most importantly, enhance the safety of your vehicle.
The Role of Brake Calipers in Overall Brake Performance
Brake calipers play a critical role in overall brake performance, working together with the brake pads and pistons to slow or stop your vehicle. A brake caliper is responsible for housing the brake pads and pistons, which apply pressure to the brake rotor to slow or stop the vehicle.
When a brake caliper is installed correctly, it can provide optimal braking performance, including improved stopping power, reduced brake fade, and increased safety. However, when a caliper is installed incorrectly, it can lead to reduced braking performance, uneven brake pad wear, and increased risk of accidents. Properly functioning calipers ensure that the braking system operates efficiently, providing the necessary stopping power to keep you and your passengers safe on the road.
Why Choose DFC Newly Manufactured Calipers?
With a catalog of nearly 3,000 SKUs, DFC offers the largest selection of new brake calipers in the industry. Our calipers are designed to address the challenges posed by remanufactured units, including:
- No core returns or hidden charges.
- Precision-machined components for easier installation.
- Corrosion-resistant coatings for durability.
- Compatibility with modern technologies like EPB and integral parking brakes.
Additionally, we’ve recently reduced prices by 10.94%, making our calipers more cost-effective than ever. Shops can now enjoy the benefits of new calipers at prices that compete with remanufactured alternatives—without sacrificing quality or performance. DFC calipers are designed for easy and accurate connection to the brake line, ensuring reliable performance.
Upgrade Your Brake System with DFC Calipers
Don’t let the inefficiencies of remanufactured calipers slow your shop down. DFC’s newly manufactured brake calipers provide reliable performance, easier installation, and long-term durability, all while eliminating core returns and other hidden costs.
Contact us today to explore our extensive catalog and discover how DFC calipers can enhance your operations and customer satisfaction.