Testimonial Tuesday is back!
Today we’re talking DFC with Bryan from Ken’s Auto Center in San Diego, CA.
“It’s really important that we get as close to an OEM as we absolutely, possibly can,” says Bryan. He explains that both the material and craftsmanship of DFC is “top notch.”
Click the video below to watch the testimonial.
Pricing is one of the pain points of customers everywhere.
As Bryan mentions, there is variation between a full factory fit and an economy-style rotor. To save money, customers sometimes prefer one over the other. That said, he considers DFC an excellent choice for either need.
As part of their commitment to serving the military and its veterans, Ken’s Auto Center plans to create a program that offers veterans a free set of DFC Brake Pads with every brake job. We wish this new program great success in braking boundaries!

Ready for your new brakes?
Click here to see our latest deals & selection
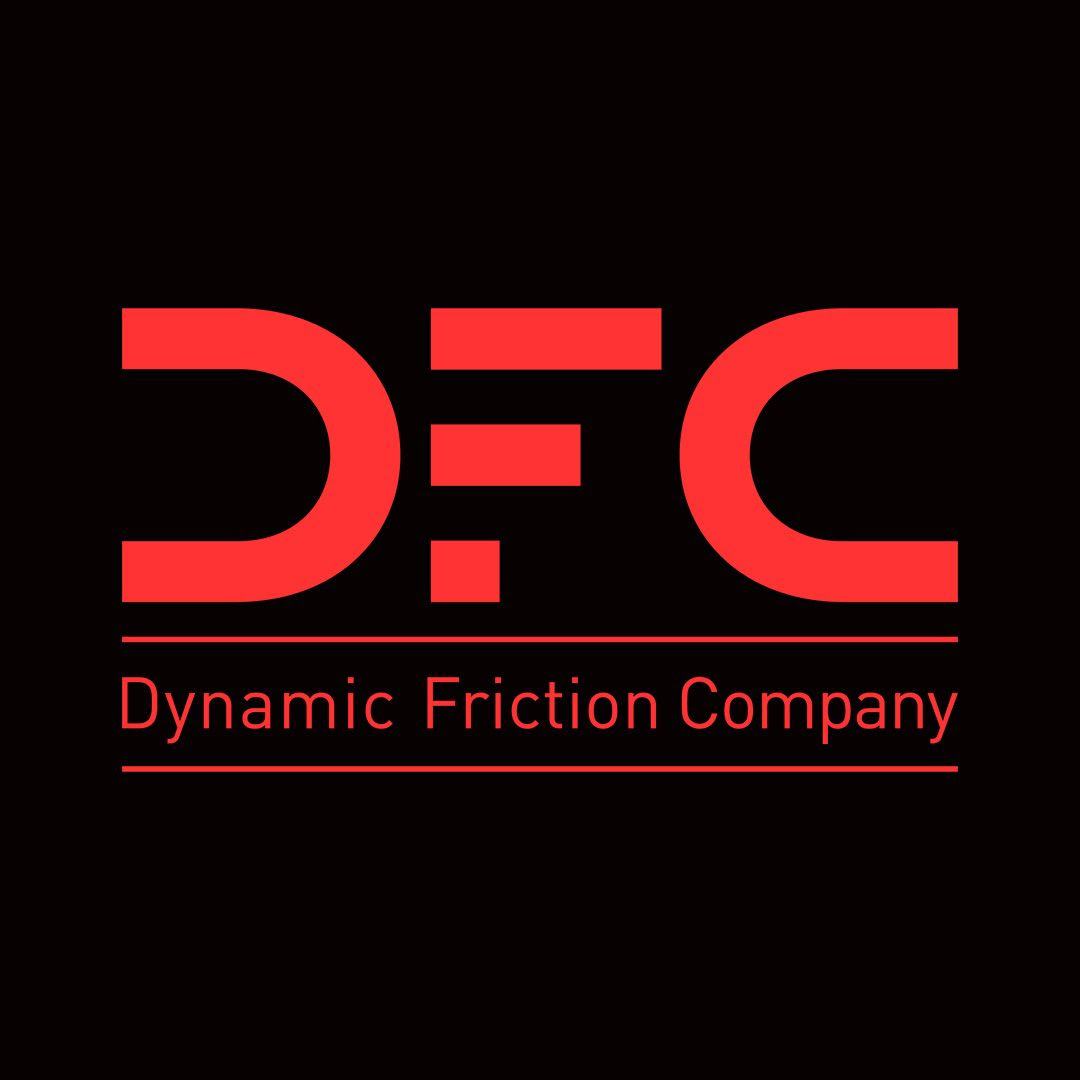