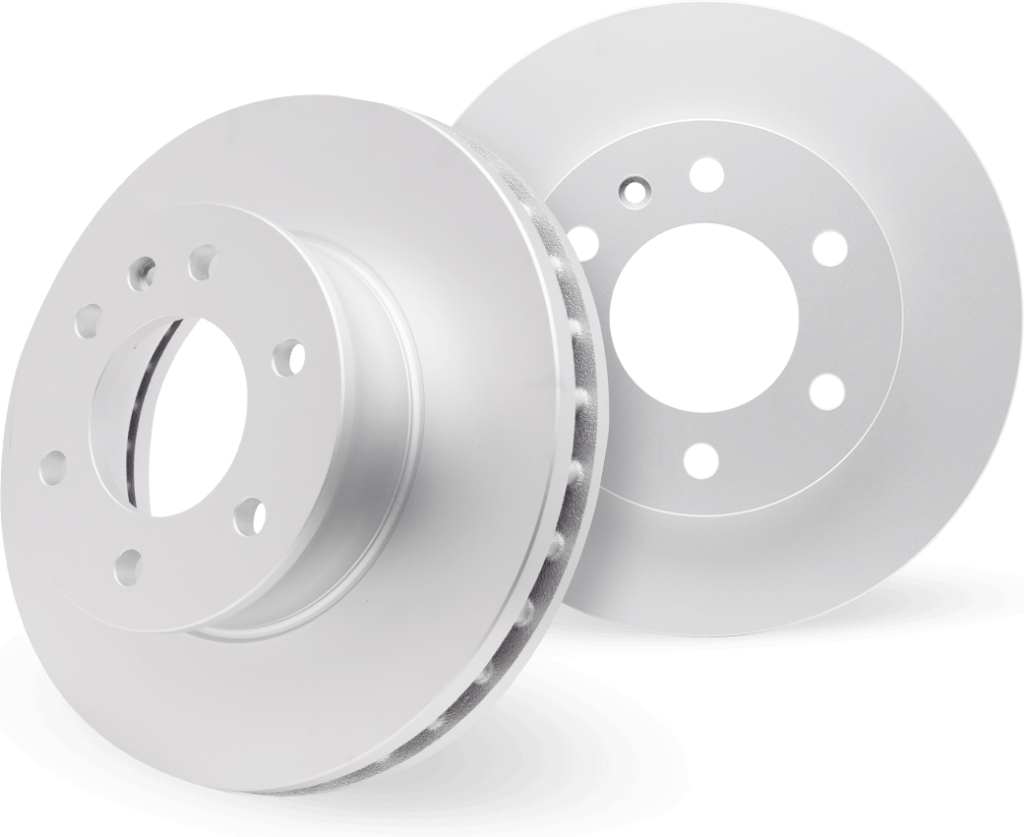
When it comes to brake performance, longevity, and reliability, achieving a balance in brake pad selection is crucial for optimal performance and disc longevity. Additionally, certain aluminium alloys containing copper affect their susceptibility to corrosion. At Dynamic Friction Company (DFC), our corrosion-resistant GeoSpec Coated Brake Rotors set the industry standard, offering superior protection and performance compared to competitors. With cutting-edge engineering and a focus on customer value, DFC ensures your braking system operates at peak efficiency for longer.
The Problem with Corrosion in Braking Systems
Corrosion can significantly impact the effectiveness and lifespan of brake components. When rotors and other metal components, including iron, are exposed to moisture, road salt, and other environmental factors, they begin to rust. This corrosion weakens the structural integrity of the rotor, compromises braking performance, and accelerates wear. For drivers, this means increased maintenance costs and potential safety risks.
Advanced Corrosion Protection Technology
In the realm of corrosion protection, advancements in technology have significantly enhanced our ability to safeguard metal surfaces. At the forefront of this innovation is the development of new materials and manufacturing processes that provide added protection against rust and corrosion. One of the most effective methods is the application of anti-rust technology, which involves coating metal surfaces to prevent rust formation.
Various types of coatings, such as epoxy, acrylic, and ceramic, offer unique properties tailored to specific needs. Epoxy coatings, renowned for their high corrosion resistance, are ideal for high-traffic areas and environments exposed to harsh elements. Acrylic coatings, known for their flexibility, are perfect for applications where the metal surface experiences movement or vibration. Ceramic coatings, on the other hand, provide exceptional heat resistance and durability.
Beyond coatings, other technologies like corrosion inhibitors play a crucial role. These chemicals, when applied to metal surfaces, actively prevent corrosion. Additionally, the use of corrosion-resistant materials such as stainless steel and titanium offers an alternative to traditional metals, ensuring longevity and durability.
By leveraging advanced corrosion protection technology, it is possible to achieve the best results in protecting metal surfaces. Whether through innovative coatings or the use of superior materials, these advancements ensure that metal components remain resilient and functional over time, providing peace of mind and reducing maintenance costs.
By following this structured approach, the new sections will seamlessly integrate into the existing article, maintaining consistency in tone and style while providing valuable information on advanced corrosion protection technology.
How DFC’s GeoSpec Coating Provides Corrosion Protection
DFC GeoSpec Coated Brake Rotors are engineered with a patented coating technology that forms a durable silver-gray finish. Unlike conventional paints or zinc coatings, our coating is specifically designed to provide superior corrosion resistance in the harshest conditions.
Key features of DFC’s GeoSpec Coating include:
- Enhanced Rust Prevention: Outperforms standard coatings to protect against rust and environmental wear.
- Durable, Attractive Finish: The silver-gray finish maintains its appearance and performance over time.
- Ready-to-Install Design: Processed and shipped dry, eliminating the need for additional cleaning or preparation.
- Weight Management: Helps manage the weight of the braking system, reducing strain and enhancing performance.
What Sets DFC Apart from the Competition
- Patented Technology: While many competitors use basic zinc or paint coatings, DFC’s patented solution provides longer-lasting and more effective protection.
- Non-Directional Finish: Promotes quicker and more even brake pad bed-in for smoother stops and reduced noise, enhancing overall braking speed.
- High Carbon Content: Improves durability, noise dampening, and overall rotor performance.
- Industry-Standard Compliance: GeoSpec rotors meet or exceed the highest quality standards, ensuring safety and reliability for all vehicle types.
Benefits for Drivers and Technicians
For vehicle owners, DFC GeoSpec Coated Brake Rotors mean fewer replacements and greater peace of mind. Technicians benefit from the time-saving ready-to-install design, reducing labor costs and improving efficiency in the shop.
Proven Performance Across All Applications
DFC’s GeoSpec Coated Rotors are ideal for a wide range of vehicles, from daily drivers to heavy-duty applications. Whether you face harsh winters, frequent road salt exposure, or high-performance braking demands, these rotors provide unmatched resilience and reliability.
Choose DFC for Long-Lasting Braking Solutions
At DFC, we’re committed to innovation, quality, and value. Our corrosion-resistant GeoSpec Coated Brake Rotors outperform competitors by delivering durable, ready-to-install solutions that keep your vehicle’s braking system in top shape.
When you need brake components that stand the test of time, DFC is the name to trust.